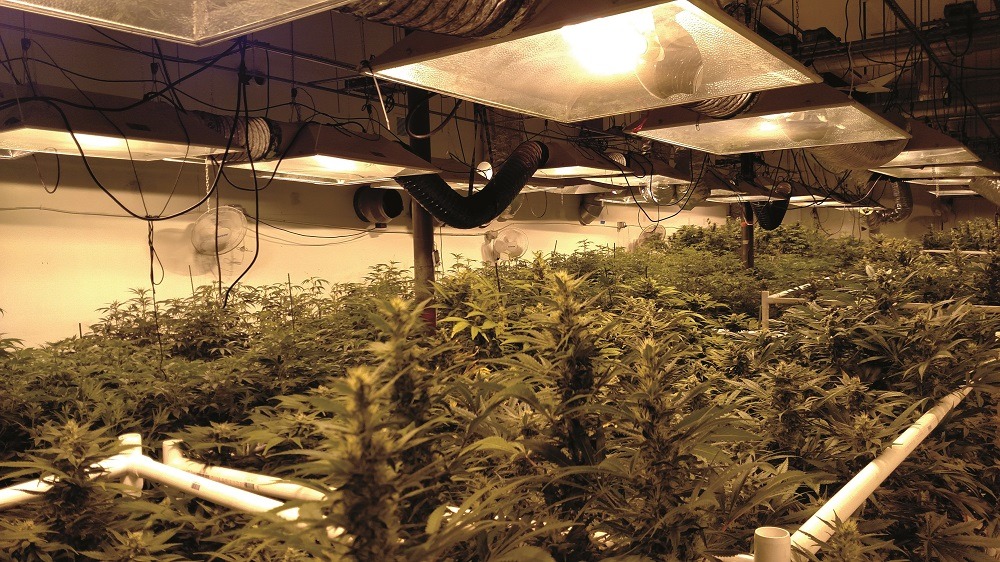
According to some indoor growers, a CRAC unit and proper HVAC sizing can lead to four to five pounds of flower per light.
What limits a cannabis plant from achieving its maximum growth potential? What is the maximum yield that a cultivator can achieve in a single harvest? The answer relates directly to the indoor environment.
Cannabis is a weed and it will grow under extreme conditions. However, at the end of the day, are you getting the most out of your plants that you can?
Environmental Controls
As humans, much of our overall health is directly related to our environment and how much stress we encounter. The same goes for a cannabis plant. In marijuana cultivation, as in life, there are basically two types of stresses: positive and negative.
Positive stresses are the ones that can be introduced to cannabis plants that ultimately make them stronger and produce larger, more potent buds. Negative stresses can inhibit the plants’ ability to absorb light for photosynthesis, restrict leaf transpiration rates and make plants more susceptible to mold and mildew.
Cannabis plants are sensitive organisms. They are temperamental and moody, and they don’t like even the slightest changes in their environment. Keep your plants happy to maximize yields. Cannabis plants do not like variations in temperature during light cycles. It’s okay to change the temperature during those periods, as long as the temperature is constant and does not fluctuate. Plants will stress or go dormant when there is even a slight change in temperature. Higher temperatures can create more stress on a plant during the lights-on cycle than lower temperatures can during lights-off. Of course, growers are trying to find that ideal range to relieve stress and release maximum potential.
Typically, between 74 and 78 degrees Fahrenheit is a good starting point, but it varies between the types of strains being grown.
Humidity is another component to relieving negative stress. Lower humidity levels can allow for higher transpiration rates and decrease the potential for mold, powdery mildew or Botrytis cinerea. With high humidity levels, plants can experience vapor pressure deficit (VPD). The higher the moisture content in the air, the less the plants can transpire through their stomata. This creates additional stress on the plant. Usually between 45-50% relative humidity is ideal. Again, it’s important to emphasize as little variation as possible. Dehumidification systems must be able to maintain a humidity set-point. It’s also recommended to maintain a single humidity set-point for both the lights-on and lights-off cycles. If the humidity fluctuates even slightly during those cycles, it will create negative stress and the plants will react accordingly.
The idea is to create an environment that is as stress-free as possible. An environment with too many negative stresses can result in genetic abnormalities, such as hermaphroditism, and entire rooms or crops can be lost. What value can be put on the potential loss of a crop compared to what would be spent on HVAC systems to control the environment? What lost opportunity costs were incurred when a harvest produced two pounds per light or less?
The HVAC equipment’s size and level of control will determine the level of stress that is created in the growing environment. One major factor many growers might not be aware of is that their HVAC system is controlling to a set-point rather than maintaining a set-point. This type of control is standard in commercial air-conditioning units. Another problem is that commercial air-conditioning units do not dehumidify. There are some exceptions to that rule, but even those types of air-conditioning
units that also dehumidify do not maintain a constant level of humidity, but rather control to a humidity set-point.
Think about a home furnace or air-conditioning unit. If the thermostat is set to 74 degrees, the furnace will provide heat until that set-point is met and then shut off. It will remain off until the temperature drops out of range, then the furnace kicks in and bring the room back up to its set-point. The same holds true for an air conditioner. The industry standard for a compressor to cycle is typically 90 seconds, meaning that once the room reaches the cooling set-point the compressor will shut off and remain off for a period of 90 seconds. Think about how much temperature variation a flower room will experience during 90 seconds when the lights are on. It can be as much as 7 degrees Fahrenheit. With this type of fluctuation, plants can experience stress that growers are not even aware of. The same goes with commercial dehumidifiers. Humidity fluctuations can be as much as 10-20%. These fluctuations occur during all light cycles for the entire cultivation process. Growers might not notice fluctuations in temperature and humidity levels, but plants definitely do.
What is the solution?
Several years ago, grow facility engineers began installing computer room air conditioning (CRAC) units in flower rooms. Growing cannabis indoors combines the 24/7 mission critical demands of a data center with the humidity control of a small indoor swimming pool. As cultivators have evolved in their knowledge of indoor cultivation, they are now realizing precise indoor environmental conditions for both lights-on and lights-off cycles is the most important factor for optimal plant growth, reduced instances of VPD and mold or powdery mildew. So, if the target conditions for growing indoors are known, then why are there issues with HVAC designs?
There are four major factors that must be considered when designing HVAC systems for flower rooms: size, control, reliability and cost.
 Size
Size matters. Unfortunately, most HVAC systems for an indoor grow are undersized. And undersized systems cannot maintain precise environmental conditions that cultivators need to maximize plant harvests.
Many engineers use HVAC sizing techniques based largely on rule-of-thumb calculations and load estimates, but often fail to consider “sensible load” and “latent load.” For flower rooms, the sensible load is the load generated by the lighting, equipment and people. The latent load is associated with the amount of water in the room. Since dehumidification is achieved through the air-conditioning process, the total load is based on the sum of those two factors. Almost anyone can calculate the sensible load inside a grow room by adding up all the heat-generating components in the space, such as grow lights, equipment, people, etc. However, the latent load required for proper moisture removal after plant transpiration is the unknown variable. This leads to higher relative humidity levels in flower rooms, eventually contributing to VPD, mold or powdery mildew growth.
To properly size the HVAC system of an indoor grow, the combined sensible and latent loads must be calculated and utilized correctly. One methodology is using the sensible heat ratio (SHR) calculation:
SHR = Hs / Ht or Hs / (Hs + HL)
- SHR = Sensible heat ratio
- Hs = Sensible heat gain (lights, equipment, people)
- HL = Latent heat gain (water vapor)
- Ht = Total heat gain (sensible+latent)
The SHR is used to quantify the ratio of sensible load (cooling) to latent load (dehumidification) necessary for determining the total load. A lower SHR value means the dehumidification requirement will be higher and the supply air leaving the cooling coil should be at a lower temperature. There must be more cooling coil surface area overall to meet the dehumidification needs of the plants.
Targeting 50% relative humidity or less in flower rooms will minimize the incidences of VPD, mold and powdery mildew. The SHR is best used for this calculation, by mechanical engineers during HVAC equipment sizing and system design.
“By maintaining such precise temperature and humidity levels in our flower rooms throughout the grow cycle, the plants experience no stress and flourish up through harvest,” Igadi head cultivator Kevin Crane says.
However, without the correct sensible heat ratio, cultivators will experience the frustrations of higher humidity levels, higher incidents of VPD, mold growth and lower yields.
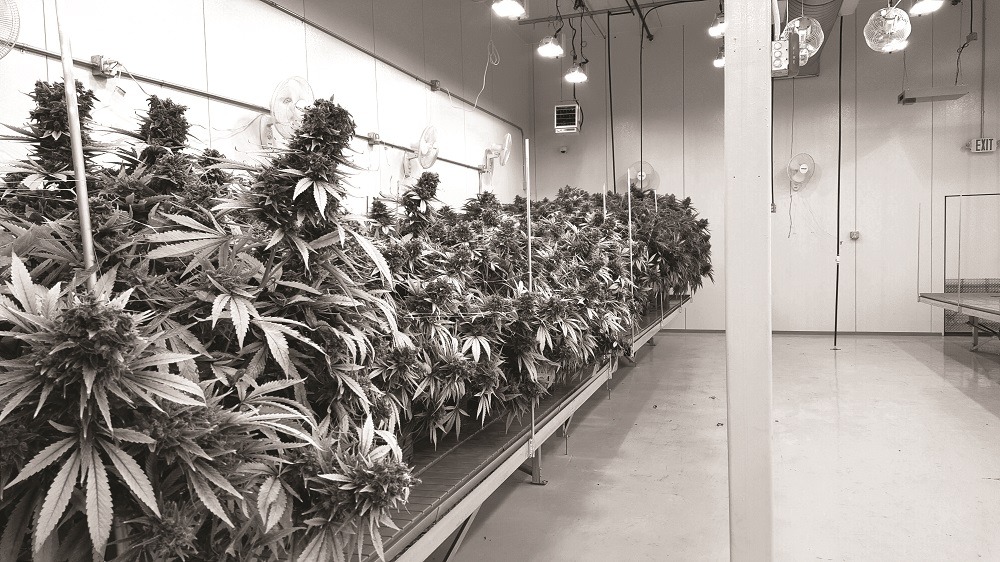
A CRAC system can help keep temperamental and moody
Control
When deciding what types of environmental systems to install in a flower room, it must be decided whether steady, precise control of temperature and humidity will be required, or if variations and fluctuations will be accepted.
Using CRAC units allows multiple units to operate and be controlled in tandem, and individual units
can be set up for either temperature-primary or dehumidification-primary for operation. This synchronized control strategy allows temperature and humidity set-points to be maintained without fluctuation. This is something typical commercial comfort cooling HVAC equipment is not capable of doing.
Reliability
Commercial “comfort” and “process” cooling are two industry terms that apply to the types of equipment used in grow facilities. The majority of the existing grow facilities have standard commercial comfort cooling HVAC systems (rooftop units, split systems) to serve the flower rooms. These systems operate sufficiently for a period of time, but are not really constructed to meet the 24/7 demands of a grow facility. CRAC units fall under the category of commercial process cooling units. Data centers have been using CRAC units for the past 40 years. Data centers, much like grow operations, potentially have millions of dollars of product sitting on the floor, meaning environmental stability is crucial. CRAC units are designed for the long-term operational demands that a grow facility presents.
In the long term, commercial comfort cooling systems will require higher maintenance and more
frequent replacement.
 Cost
This is probably the most significant factor when determining the type of environmental control for flower rooms. However, the difference in cost between commercial comfort and process cooling systems are not as substantial as one might think.
The marijuana growing industry has now gotten the attention of the CRAC unit manufacturers. There are now CRAC units that are being built solely for the marijuana cultivation industry using the same types of units with some enhancements, such as CO2 distribution and control, and bi-polar ionization to help with air-borne pathogens and odors. Considering the cost of all the individual components (air conditioners, dehumidifiers, CO2 controllers, filters, etc.), CRAC units are very competitive and include temperature, humidity and CO2 controls, and air-borne pathogen/VOC mitigation all in a single unit.
Yield
So, now we can revisit the first question that was asked: What limits the potential for maximum growth in cannabis plants? The limits are based solely on the types of stress that the cannabis plants will experience during the cultivation process. The amount of stress correlates directly to how the environment is controlled and maintained in the flower rooms, which can be tremendously improved with a CRAC unit maintaining temperature and humidity levels.
Some cultivation facilities have reported yields as high as four to five pounds per light. If the industry standard is two pounds per light, growers may be able to double their productivity without adding a single square foot of space.
As the price of marijuana continues to drop, maximizing yields is becoming more and more important, and the requirement for uncontaminated plants is increasing as well. The need for proper HVAC sizing
and control is paramount to achieve the full potential of cannabis plants.
Brian Zimmerman is the president of Impact Engineering and founder of www.grow2guys.com. Impact Engineering has provided mechanical and electrical engineering, design and consulting on more than 300 cannabis cultivation, infused product manufacturing and extraction facilities both nationally and internationally.
[contextly_auto_sidebar]